Challenge
A large healthcare products manufacturer in the United States needed to improve its environmental impact while substantially reducing excessive costs associated with municipal discharge and the operation of cooling towers.
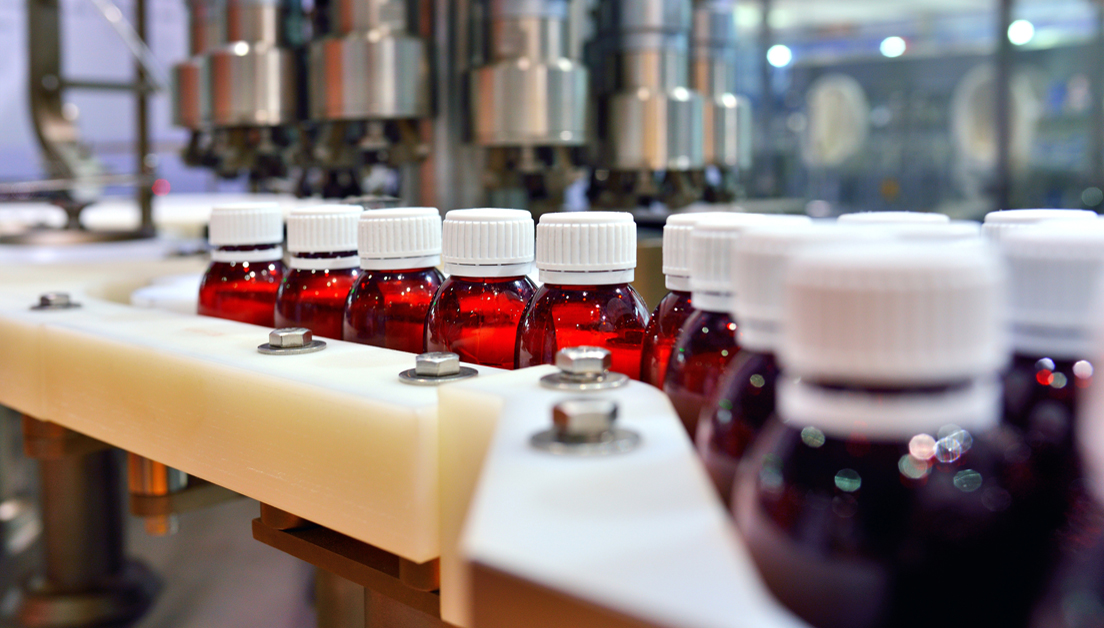
The existing purified water system included pre-filtration, activated carbon, two-pass reverse osmosis (RO) units and polishing deionization. While the existing system was operating efficiently, the size of the system resulted in a nearly continuous waste stream during its seven-day operation period. This resulted in periods of complete recirculation when the purified water product was not needed, causing unnecessary additional costs. Also, the feed water to the existing system was high in total dissolved solids (TDS), causing the waste stream of the RO to have a very high TDS level and conductivity.
Solution
Evoqua Water Technologies worked with the manufacturer to design a solution that would meet all project goals and could be carefully integrated into the existing infrastructure without operational risk, eliminating unnecessary and costly downtime. The solution was also designed to significantly lower the waste stream of the existing water system and produce high-quality feed water to the plant’s cooling towers.
A new waste treatment RO system was engineered, built and installed in the facility to achieve these goals. To address the unnecessary continuous recirculation, the system was designed to operate only when needed, and would be shut down/by-passed when not needed by detecting when the waste stream quality was adequate for cooling tower feed. This helped to further increase the efficiency of the waste treatment solution.
Key goals for the project included:
- Reduce the existing waste stream from 64 GPM to 42 GPM continuously
- Reduce waste produced and feed water required for product production to lower costs, increase efficiency and raise the level of environmental stewardship
- Filter 42 GPM of the waste stream to be sent to the cooling tower array
- Improve the water quality to the cooling towers to reduce blow-down and potentially reduce chemical costs associated with cooling tower operation
Results
The new system now operates only when needed, lowering the waste disposal and cooling tower feed requirements, with the following results:
- The waste system operates approximately 8 hours per day
- Reduced waste stream by more than 8 million gallons per year
- Reduced plant’s waste disposal costs more than $350,000 per year
- Waste disposal system has ability to operate more frequently if water quality or plant expansion dictates, further increasing the system’s return on investment
The manufacturer is extremely pleased with the process improvements, increased efficiency, lower water needs, lower waste disposal and improved cooling tower operation—all helping to lower costs and improve the company’s environmental impact.