Filter 0
Technology
0Chlorine Capacity, Maximum: kg/hr
0Carbon Dioxide Capacity, Maximum: kg/hr
0Sulfur Dioxide Capacity, Maximum: kg/hr
0Ammonia Capacity, Maximum: kg/hr
0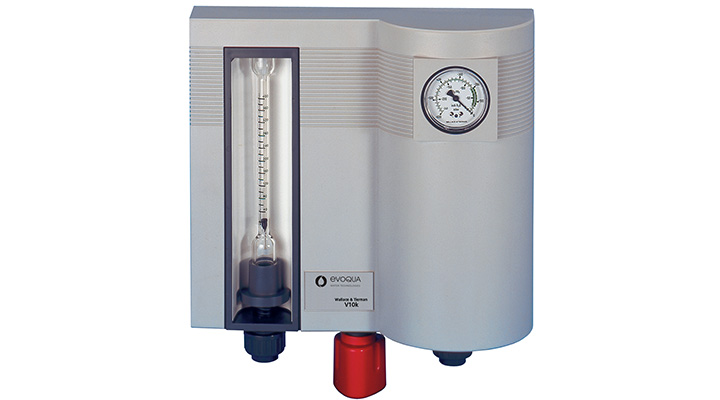
Gas Feed V10K™ Vacuum System
Efficient, low-capacity differentially regulated gas feeder with a standardized, flexible design for dosing up to 15 kg/hr
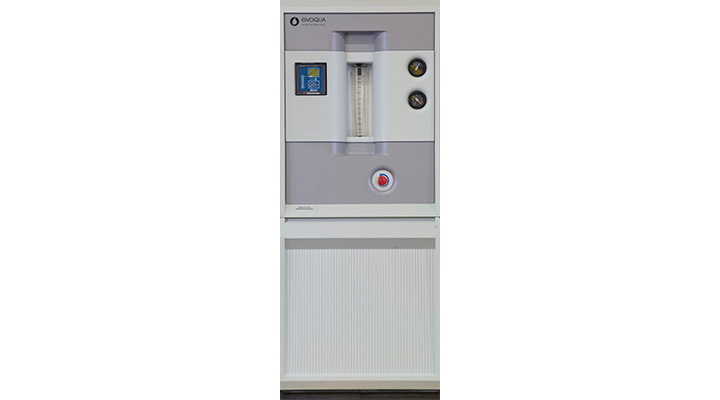
Gas Feed V-2000™ Chlorinator
Remote vacuum solution covering medium to high capacity applications with differentially regulated gas feeder and floor or wall mounted options for versatility
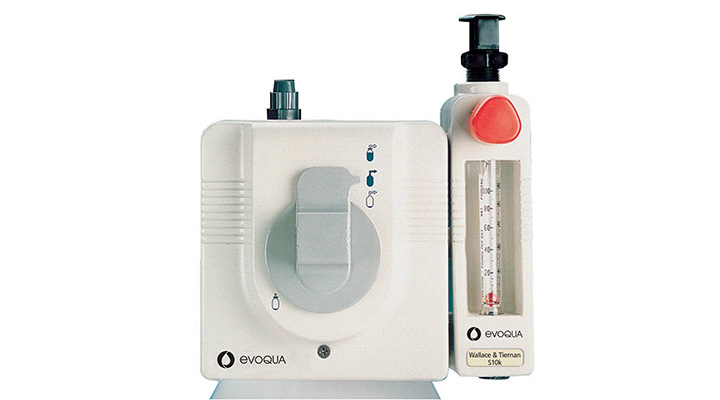
Gas Feed S10K™ Chlorinator System
All vacuum operated, sonically regulated gas feeder unit for low capacity dosing applications
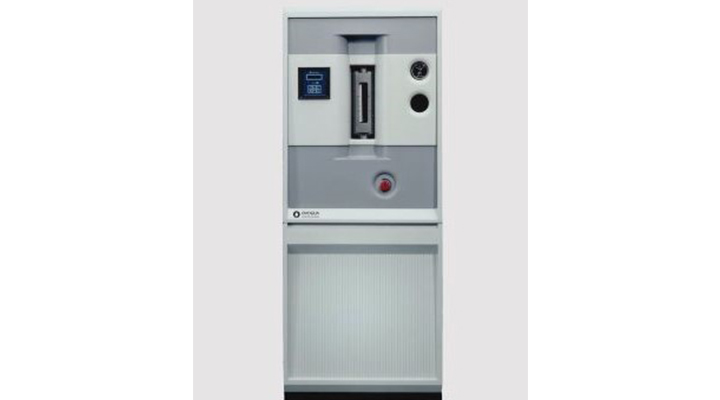
Gas Feed 60-225 Ammoniator
Control device for accurate metering of gaseous ammonia feed directly into water under positive pressure.
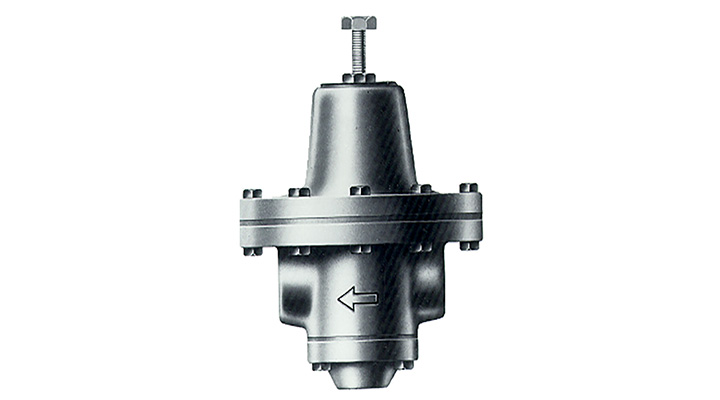
Gas Pressure Reducing Valve Series 50-165
The Gas Pressure Reducing Valve is an independent, heavy-duty, spring loaded diaphragm valve, providing an automatically regulated output and a positive manual shut off.
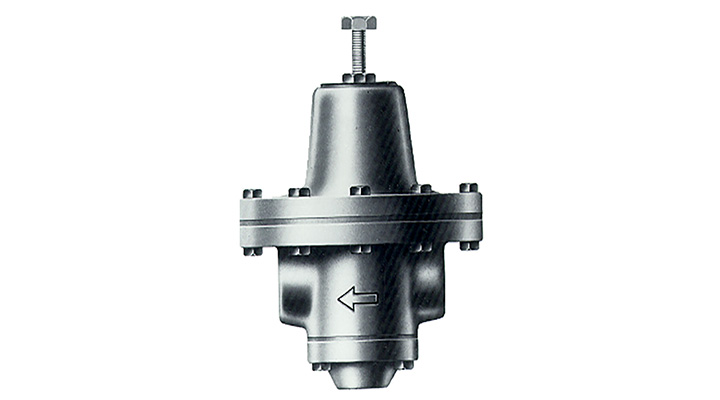
Gas Pressure Reducing Valve Series 50-185
The Series 50-185 Gas Pressure Reducing Valve (GPRV) is a spring-loaded, diaphragm operated valve used in gas-handling systems which reduces varying gas pressure to a desired regulated pressure and maintains within close limits.
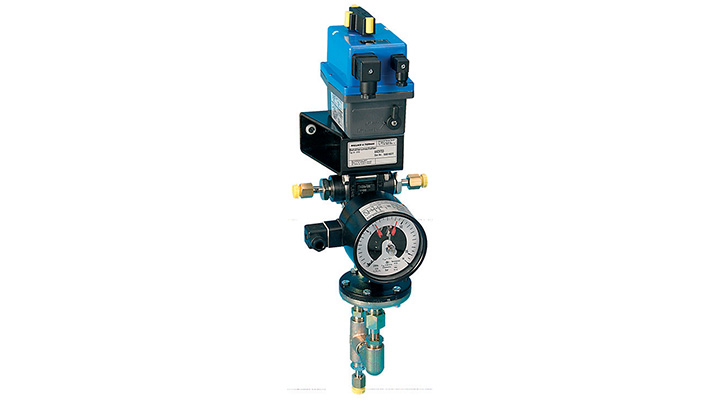
Pressure Type Changeover Modules with CCU
Evoqua offers various automatic changeover modules to ensure an uninterrupted and unattended changeover to a fresh gas supply when the on-line supply is exhausted.
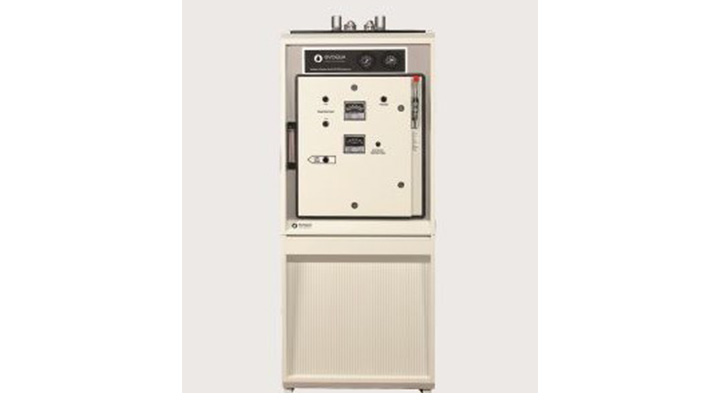
Series 50-200 Evaporator
The Wallace and Tiernan® Evaporator Series 50-200 is an electrically heated, immersed tank-type heat exchanger. It is necessary wherever the required rate of gas withdrawal cannot be satisfied by direct connection to multiple containers
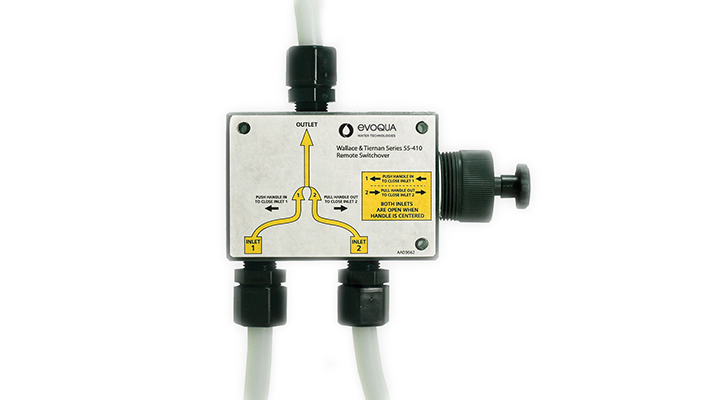
Vacuum Type Remote Switchover
Remote vacuum switchover unit which ensures uninterrupted chlorine dosing by delivering a continuous supply